Obtain news and background information about sealing technology, get in touch with innovative products – subscribe to the free e-mail newsletter.
27.06.2023 | Press release
A Union of Opposites: Heat-Conductive and Electrically Insulating
Weinheim, June 27, 2023. It has exceptional technical talent: A silicone material that is thermally conductive, electrically insulating, and suitable for injection molding. It also adheres to widely used substrates like plastics, aluminum and copper and compensates for rough areas. This “Thermal Interface Material” (TIM) has been in the portfolio of Freudenberg Sealing Technologies for some time. It has already proven its extensive suitability in several customer projects in the automotive industry.
The most universal applicability: That was the goal of Freudenberg Sealing Technologies in developing this new elastomer. It combines seemingly incompatible properties, since it is good at conducting heat while also providing electrical insulation. What all the customer projects have in common is their enormous complexity.
For example, the charging port of an electric car. A well-known car manufacturer has already used this in high-quantity series production for quite some time. Behind the charging port cover, the vehicle displays a usual multi-pin connector for the charging cable, embedded in a plain plastic front. What remains invisible is the high-tech area right behind it. Here are several components whose interaction is essential for the thermal management of the charging process. That is why the acquisition of thermal data is key to success: The temperature is tapped via the integrated novel “Thermal Interface Material” (TIM). It is directly connected to a sensor system via the housing, which processes the signals with the help of the high thermal conductivity of the TIM via measurement and control electronics. The heat flow data can only be obtained by means of the best possible heat transfer combined with the highest possible insulation of the material in thermal management systems. The TIM can be used at electrical voltages of up to 800 volts.
The two-component plastic housing has a complex three-dimensional geometry, as it ensures clearances and creepage space. Clearance is the shortest distance between two conductive parts. The creepage space is the shortest distance along the surface of an insulating material. Freudenberg Sealing Technologies manufactures the housing with injected elastomer and provides it to an automotive supplier, which in turn produces the module ready for installation by the automaker. The latter installs it in large numbers in series-produced vehicles.
Predestined for complex applications
“TThis project was right up our alley, because our material is predestined for a wide range of complex electrical applications. With its numerous qualities, it provides the right answers,” says Armin Striefler, Product and Process Developer at Freudenberg Sealing Technologies. “An important advantage for efficient series processes: The elastomer material can be processed through injection molding. This also makes its use very flexible, since nearly all three-dimensional geometries are possible and, thanks to its the material properties, always adhere optimally to the substrate – whether plastic or metal. It can be sprayed on directly and doesn’t need primer."
Like all plastics, silicone is inherently thermally insulating. For the new material, it is mixed with inorganic fillers that make it thermally conductive. These fillers are special non-conductive metal compounds.
Top values for important key figures
A few key figures for the innovative thermal interface material: Thermal conductivity is 1.7 to two watts per meter-Kelvin. For comparison, the thermal conductivity of air is 0.026. The manufacturing process makes thin-walled components possible. According to the heat equation from Fourier equation, this is good for thermal conductivity. In the above-mentioned project, the elastomer below the temperature sensor has a thickness of only 0.8 millimeters. “We have had very good experiences with thicknesses between 0.8 and three millimeters,” reports Striefler. “For physical reasons, heat transfer decreases when the walls are thicker.” The material achieves a CTI value of 600, placing it in the best possible protection class for tracking resistance. The dielectric strength is more than 10 kilovolts per millimeter. This means that the common test voltages of 2.4 to 4 kilovolts won’t pose any particular challenges for the material. Its hardness is around 35 Shore A.
Being able to use an injection molding processes is a definite plus. The specific production process prevents trapped air both in the elastomer and on the contact surfaces with other materials. This might otherwise lead to electrical problems, such as voltage breakdowns – which are certainly not welcome, of course. The material is fire-resistant in accordance with UL94 with classification V0, which puts it at the highest possible safety level.
Wide range of applications
Effective heat dissipation is a prerequisite for efficient processes in numerous electrical applications – wherever considerable computing power is required, or high currents are flowing. At this time, typical applications are in the field of electromobility, not least because of the significant requirements when the charging voltage is 800 volts, which is increasingly common in electric vehicles. Cooled busbars in traction batteries are one example. Especially during fast charging or high-power output, these heat up with relatively high intensity.
The material and process are predestined for the targeted heat discharge of technical components. With a three-dimensionally designed molded part, this can occur in direct contact with the electronic components. The range of applications is vast. This is evident in the example of an oil-resistant TIM that is currently in pre-development at Freudenberg Sealing Technologies. A material like this goes even further in expanding the potential applications. “We welcome tricky challenges,” Striefler concludes. “Because that’s exactly where this material is in its element.”
Ulrike Reich
Head of Media Relations & Internal Communications
Telephone: + 49 (0) 6201 960 5713
ulrike.reich@fst.com chevron_rightNews Service
You can subscribe to the Freudenberg Sealing Technologies news alert service, bringing you the news as soon as they are published. You can always unsubscribe from this service.
Subscribe now! chevron_rightMore news on the subject E-Mobility
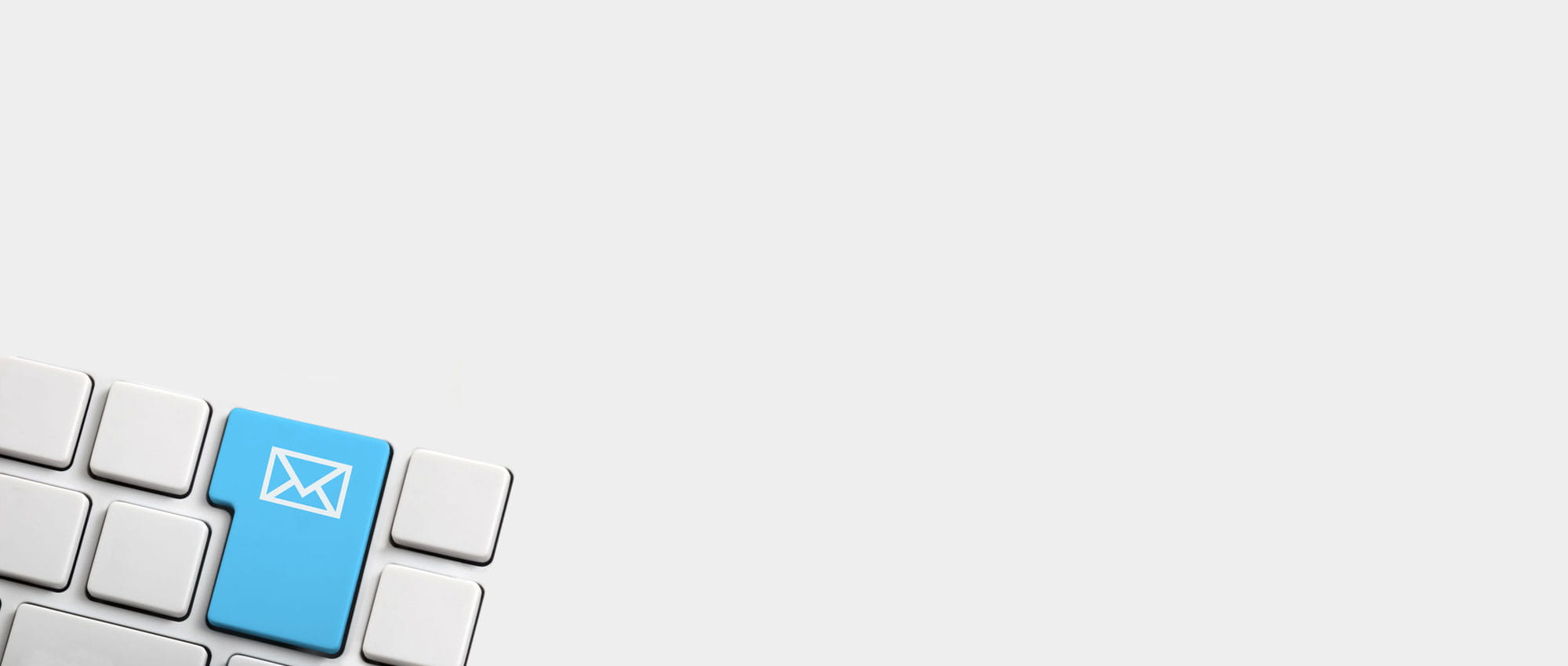
News Service
You can subscribe to the Freudenberg Sealing Technologies news alert service, bringing you the news as soon as they are published. You can always unsubscribe from this service.
Subscribe now!