Obtain news and background information about sealing technology, get in touch with innovative products – subscribe to the free e-mail newsletter.
14.11.2023 | Press release
Flexible, wear-resistant and minimal frictional losses
Weinheim, November 14, 2023 – Flexible and wear-resistant with minimal frictional losses – those were the requirements presented to Freudenberg Sealing Technologies for the development of a new seal for use in cobots. The versatile robotic arms thus became the driver for a complete redesign.
Today’s industry can no longer get around the use of cobots. These flexible, fast machines work hand in hand with people in many activities. One of the key requirements is that they must be adaptable enough for use in different work environments, and not just handle a range of tasks. Robots used in a welding cell today, for example, should be able to work on a packaging line a week from now. This puts significant demands on the application profile for the popular manufacturing helper.
Competitive Advantage Due to the Right Seal
That’s why one manufacturer was looking for a sealing solution to protect all its cobots’ joints from dust, spraying water and other contamination reliably and over the long haul. Simple PTFE rings have been used to this point so efficiency, energy consumption and the robotic arms’ speed of motion are not overly compromised. However, the rings were not able to guarantee the required IP54 protection class. High travel speeds and the forces generated in the robot arm also create an environment with temperatures as high as 60° C (140 °F). A seal not only has to withstand these temperatures long-term – extremely low material elongation is important as well, to guarantee functionality in each operating mode and at all temperatures.
The development partner turned to Freudenberg Sealing Technologies (FST) due to its outstanding reputation and development expertise. As a first step, the sealing experts presented a u-ring made of polyurethane (PU). But in practical tests, the frictional forces proved to be too great due to its relatively large surface. Those forces were not supposed to exceed 1 newton meter. This extremely low value made it necessary to significantly reduce the radial forces and at the same time also of contact stresses on the dynamic seal lip.
A New Development Meeting Stringent Requirements
So in the next step, the sealing experts changed the overall geometry to a z-profile and integrated a second groove. This greatly reduced the contact pressure and met the requirement for a moment of friction of less than 1 newton meter. In the practical test, however, the level of wear was still far too high. This was mainly due to the cobots’ lightweight, largely aluminum construction. The surface of the material is relatively rough due to the methods used during its processing and its basic characteristics. As a solution, Freudenberg Sealing Technologies developed a three-component solid film lubricant coating with high carbon content. The coating made it possible to further reduce the amount of wear.
With a Shore hardness of 92, the material in question, 92 AU 21101, is very soft and flexible. Nonetheless, its tensile strength is 59 MPa, putting it significantly above the required minimum level of 50 MPa. At minimal elongation, components made of 92 AU 21101 can be relied on in temperatures ranging from -50°C to +110°C. Their conformity with RoHS, 2015/863/EU and 2011/65/EU is unrestricted and unconditionally valid.
Development Expertise Meets Express Service
In response to changes in the cobot’s design, the seal geometry had to be completely reworked once again. For the final version, Freudenberg Sealing Technologies selected a z-geometry with a further optimized dynamic seal lip. A static area with a groove was constructed externally. Thanks to the systematic use of FEA calculations for the lip thickness and a later simulation, it was possible to achieve significant savings as unnecessary process steps were eliminated.
The implementation with the help of Freudenberg Xpress® as a service provider offered fast responses and short development times throughout the process. Freudenberg Xpress® produces affordable, high-value CNC-turned sealing solutions. It not only manufactures prototypes – it handles small production runs and one-offs economically and quickly as well. Here Freudenberg Sealing Technologies applies the same standards that it uses for large-scale production. It has established processes for quality assurance and lab testing, along with comprehensive on-site service in much of the world. This enables Freudenberg Sealing Technologies to design, simulate and deliver solutions in the event of requirement modifications within two weeks.
Creating a new best practice, the robot manufacturer has decided to integrate partners such as Freudenberg Sealing Technologies into the development process for its products at a very early stage. Their collective experience makes it possible to consider many additional parameters in advance, which leads to shorter development times and fewer correction cycles. The product is also ready for the market sooner.
Product developer Alexander May summed up the advantages of combining in-house development expertise with the services of Freudenberg Xpress®: “We can react and deliver the product quickly. That is not just a real advantage that our customers appreciate during periods of global bottlenecks. We arrive personally on site in short order and work directly on the specific challenges worldwide, which always results in positive feedback. In a world of highly automated mass production, we are active in an area that many other manufacturers do not find attractive: one-off products and short production runs. When this is combined with our knowhow and the same quality standards as with large-scale series production in the millions of units, it is a door opener.”
The bottom line for the robot manufacturer: The company is extremely gratified with the results of the development work. Thanks to the development expertise of Freudenberg Sealing Technologies, the range of applications is now much wider for the cobots. The high degree of flexibility is not only keeping users happy – it is opening up new market segments as well.
Ulrike Reich
Head of Media Relations & Internal Communications
Telephone: + 49 (0) 6201 960 5713
ulrike.reich@fst.com chevron_rightNews Service
You can subscribe to the Freudenberg Sealing Technologies news alert service, bringing you the news as soon as they are published. You can always unsubscribe from this service.
Subscribe now! chevron_rightMore news on the subject Industrial Applications
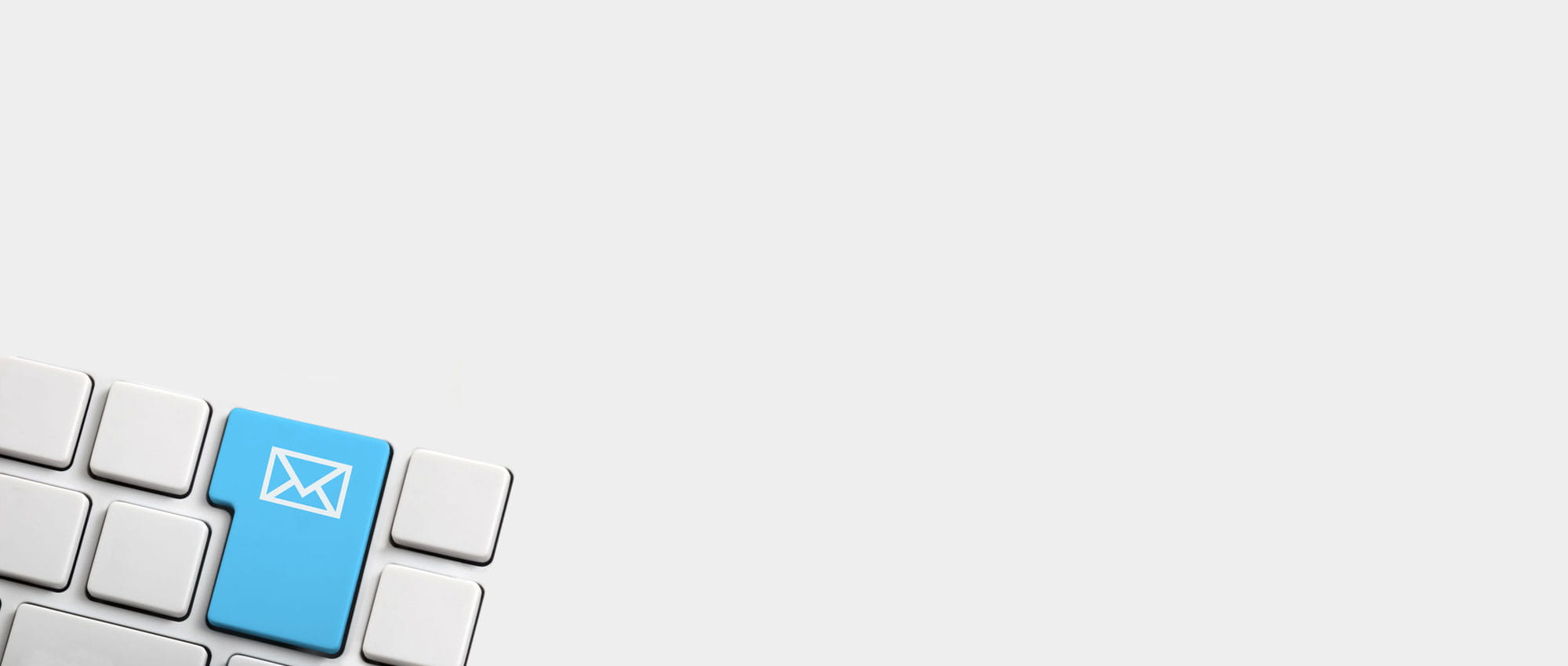
News Service
You can subscribe to the Freudenberg Sealing Technologies news alert service, bringing you the news as soon as they are published. You can always unsubscribe from this service.
Subscribe now!