Obtain news and background information about sealing technology, get in touch with innovative products – subscribe to the free e-mail newsletter.
10.04.2025
New Sealing Material For Safe Battery Cells
In the rapidly growing electric vehicle market, improved battery performance with shorter charging times, maximum temperature resistance and a longer battery life are key factors for success. To meet these demands, OEMs in Europe and the United States need materials that also comply with stricter national and international environmental standards. One high-performance material for such applications comes from the elastomer material group. Freudenberg Sealing Technologies has successfully developed a material that outperforms thermoplastics in the event of thermal runaway and takes battery applications in e-mobility to an entirely new level.
Using material advantages – elastomer seals instead of thermoplastics
Thermoplastics that are traditionally used for battery seals have macromolecules with long-chain molecular structures that are not chemically cross-linked but instead held together by weak intermolecular forces. While thermoplastics can be elastically deformed to some degree, the constant charging and discharging of the battery cell also causes them to undergo functionally relevant plastic deformation over time. This is different in elastomers whose molecular chains are chemically cross-linked. In their basic state, the polymer chains form a tangled ball that stretches or compresses under tensile and compressive loads. Due to the entropy elasticity, these cross-linked materials react elastically and reversibly, maintaining their shape exceptionally well during the cyclical volume change of the battery cells under load.
“Our O-rings made from the new elastomer therefore prevent electrolyte from leaking out of the battery cell or impurities from entering the cell,” explains David Kuhne, Application Engineer at Freudenberg Sealing Technologies. “You shouldn’t think of a battery cell as a rigid construct – it ‘breathes’. When the temperature in the battery cell rises from ambient levels to – as a rule – ranges of up to 60°C, the cell expands and then contracts in the same way as it cools. Elastomers show significant advantages over thermoplastics during this continuous stress.” explains Kuhne the charging and discharging process.
Materials expertise – from cutting-edge research to large-scale production
The development of new battery materials prioritizes sustainability as well as economic aspects. In general, the longer a battery can be used, the more sustainable the electric vehicles become. The new sealing material from Freudenberg Sealing Technologies contributes to this goal.
When used in customer projects, the new material was able to improve the performance-relevant leakage rate of the battery cells by an order of magnitude – in other words, resulting in a tenfold improvement compared to conventional thermoplastic seals.
Another essential aspect is the extreme sensitivity of battery cell electrochemistry to potential contamination. Dr. Stefan Schneider, Head of Material Development at the O-Rings lead center, explains: “Premature capacity loss, which has been observed in cells sealed with conventional elastomers, can result from minimal but still present impurities in the sealing material. The infiltration of moisture into the cell has a similar effect, as it can cause the decomposition of electrolyte components. These aspects were considered when the new material was developed.” In addition, Process Engineering has optimized manufacturing techniques to such a degree that it is possible to produce these high-performance battery cell seals in large series.
Rising demand for batteries fuels electric vehicle expansion
As a leading provider of high-performance materials and innovative products, Freudenberg Sealing Technologies is instrumental in developing safe and sustainable e-mobility. And the timing is perfect: The International Energy Agency’s (IEA) annual “Global Electric Vehicle Outlook” reveals the global developments in electric mobility. According to “Outlook 2024”, the worldwide electric vehicle fleet must expand from less than 45 million vehicles in 2023 to 250 million by 2030 to stay on track for net-zero emissions. This will also drive a sharp increase in the demand for high-performance batteries. Freudenberg Sealing Technologies is pleased: “As a development partner for customer-specific projects, we contribute many years of expertise in materials and innovation. Thanks to our advanced analytical methods and vertically integrated manufacturing processes, we can develop and implement competitive production solutions with great agility,” concludes David Kuhne.
Josh Barnett
Corporate Communications Manager
Telephone: + 1 734 354 2406
josh.barnett@fnst.com chevron_rightSilke Herzog
Senior Manager Corporate Communications
Telephone: + 49 (0) 6201 960 6385
silke.herzog@fst.com chevron_rightDownload Press Release
Download Images
News Service
You can subscribe to the Freudenberg Sealing Technologies news alert service, bringing you the news as soon as they are published. You can always unsubscribe from this service.
Subscribe now! chevron_rightFurther Articles With These Taggings
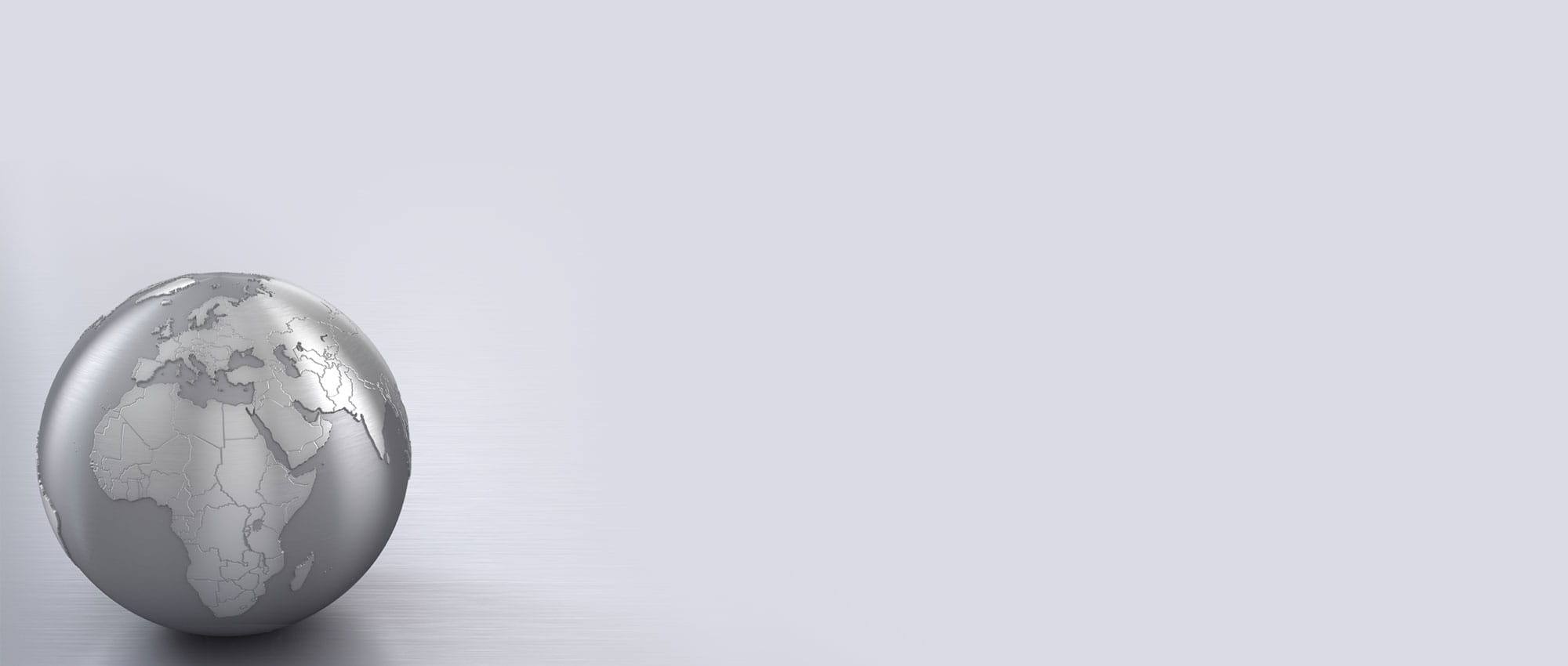
First Hand News
Best of all, keep up with the latest developments
with the Freudenberg Sealing Technologies newsletter.