Obtain news and background information about sealing technology, get in touch with innovative products – subscribe to the free e-mail newsletter.
19.02.2019
Measurements at 36,000 RPM
Seals that are used between the electric motor and the downstream transmission have to satisfy much more stringent requirements for speed-endurance strength than seals in conventional powertrains. While the internal combustion engines in cars today reach a maximum rotational speed between 4,000 and 7,000 rpm, depending on the combustion process, the figure for electric motors is significantly higher. Today electric motors for series production vehicles reach a maximum rotational speed of more than 20,000 rpm. But rotational speeds alone are not a complete expression of the total load applied to the seal. It has more to do with the circumferential speed that results from the rotational speed and the shaft diameter. In the future, experts are not ruling out speeds of up to 100 meters/second as a result of technical advances and steady increases in requirements. With a shaft diameter of 55 mm, that works out to 35,000 rpm.
Test stands with specific key characteristics
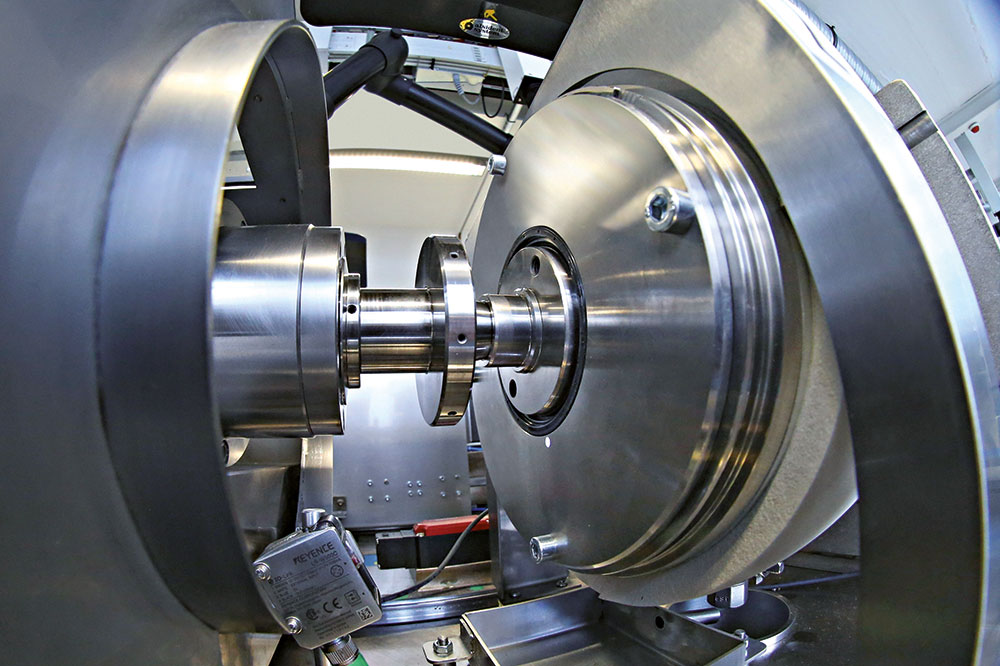
Due to their high circumferential speeds, the shaft seals that are being used in electric cars have to produce very little friction. Otherwise, the inherent high efficiency of electric powertrains would suffer, and they might show premature wear. With this in mind, Freudenberg Sealing Technologies has added several test stands to its Weinheim test facility that are specially designed to measure frictional torque in the heavily stressed shaft seals used in electric motors. To guarantee high precision in their measurements, the test stands have several key characteristics. For example, the torque is produced by water-cooled, high-rpm spindle drives – the kind commonly seen on machine tools. The test drum is equipped with nearly friction-free air bearings radially and axially so the seal’s frictional torque can be determined as precisely as possible.
The latest test stands, which just went into operation, not only permit frictional torque measurements at rotational speeds of up to 36,000 rpm – they allow the capture of the seals’ electrical impedance at a wide range of frequencies. This is important because substantial electrical potential can be generated between the housing and the shaft of the electric motor. The discharge can take place across the shaft bearing and lead to surface damage from electrical erosion. Freudenberg Sealing Technologies already offers seals that enable the voltage to be drained off across an electrically conductive nonwoven. The new test stands are an important tool for designing and validating such seals.
Frictional torque measurements for shaft seals can be undertaken on these stands and can lead to improvements in designs and materials. They are making important contributions to advances in the overall efficiency and durability of electric powertrains. When the measured frictional torque values are correlated with other values such as shaft diameter, various sealing materials and designs can be compared with one another at an early development stage. Since the friction changes – it does not remain constant -- across the rotational speed, seals can be deliberately adapted to later operating ranges before the first prototypes of the motors even exist. “With the expansion of our test facility, we are gearing up for the new requirements that lie ahead for sealing technology due to electric mobility,” said Grazyna Jedrowicz, who is in charge of global testing at Advanced Product Technology at Freudenberg Sealing Technologies.
Ulrike Reich
Head of Media Relations & Internal Communications
Telephone: + 49 (0) 6201 960 5713
ulrike.reich@fst.com chevron_rightDownload Documents
News Service
You can subscribe to the Freudenberg Sealing Technologies news alert service, bringing you the news as soon as they are published. You can always unsubscribe from this service.
Subscribe now! chevron_rightFurther Articles With These Taggings
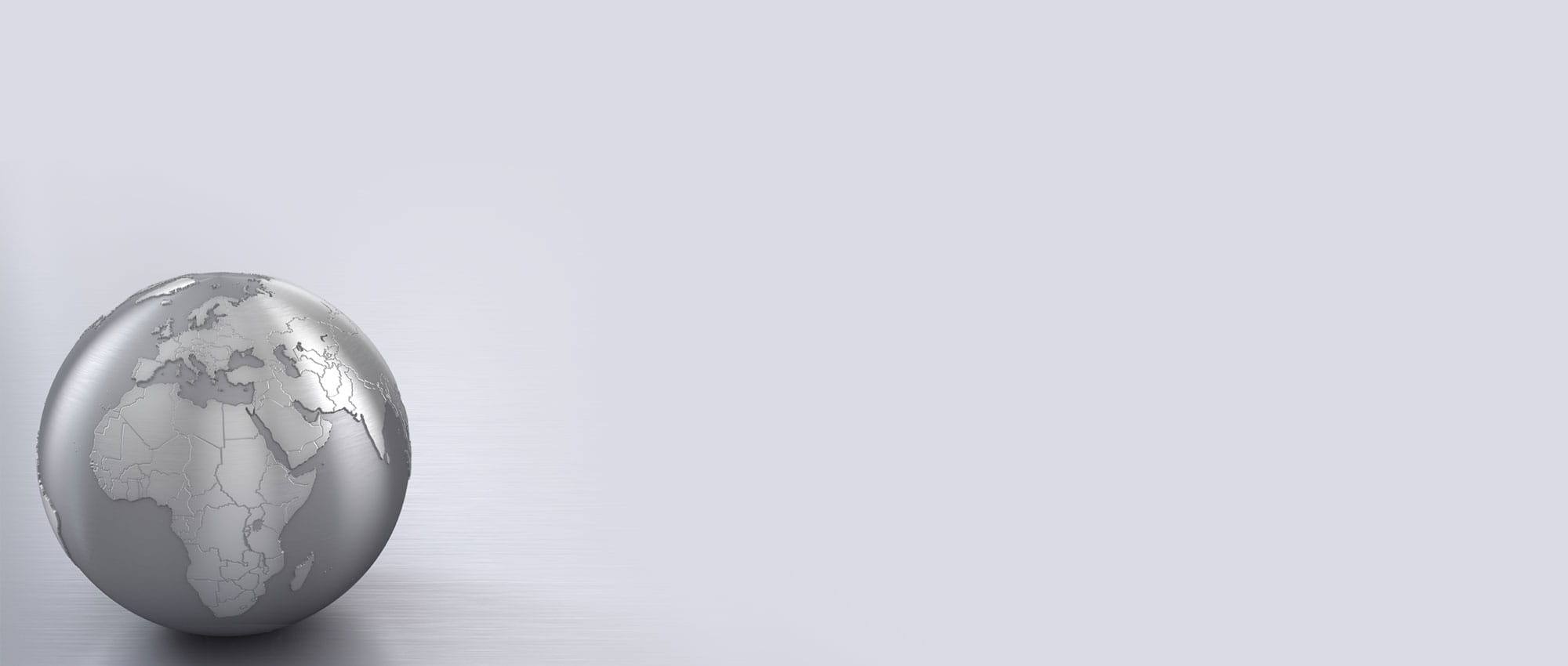
First Hand News
Best of all, keep up with the latest developments
with the Freudenberg Sealing Technologies newsletter.